As a recruiter engaging with manufacturing leaders, it’s essential to convey the unique challenges and opportunities within the industry. The distinction between being a leader and being a great leader is particularly pronounced in the fast-paced world of manufacturing. It requires a combination of technical expertise, people skills, and strategic thinking. Here are key things to consider in your journey to becoming the exceptional leader your organization needs.
- Starting with the Diagnosis and Strategy
- Unique Ability: Great leaders in manufacturing possess a keen ability to diagnose operational inefficiencies and safety concerns that others might overlook.
- Challenge: The real challenge lies in not just identifying these issues but also in developing robust strategies that enhance productivity and ensure worker safety.
- Developing the Vision and Grit
- Balance: Mastering the duality of abstract thinking and concrete action is vital. Leaders must envision long-term goals while being grounded in the day-to-day realities of the manufacturing floor.
- Perspective: Reflect on leaders who have significantly impacted your facilities; they likely had the foresight to tackle both operational challenges and employee morale.
- Breaking the Mold: No More Excuses
- Mindset: Great manufacturing leaders are made through a relentless pursuit of excellence. They understand that complacency can lead to costly errors and inefficiencies.
- Commitment: They push boundaries and challenge the status quo, often viewed as disruptors who innovate processes and improve product quality.
- Determination: In a field where deadlines are critical, they don’t take “no” for an answer when it comes to meeting production goals.
- Communication is Key
- Skill: Effective communication is paramount. Great leaders can articulate their vision clearly and inspire their teams to work towards shared goals.
- Understanding: Conveying your ‘why’—the purpose behind production targets and quality standards—is crucial for gaining buy-in from both the workforce and upper management.
- Joint Ownership: Foster a culture of joint ownership where employees feel responsible for not just their tasks but the overall success of the production line.
- The Real Test: Adaptability
- In Remote Work: With advancements in technology, remote work has become more prevalent, even in manufacturing. Leaders must adapt to these changes while ensuring that team cohesion and communication remain strong.
- Connection: Establishing strong connections with team members, whether on-site or remote, is essential for maintaining morale and productivity.
- Focus: Avoid letting corporate jargon obscure real goals. Focus on what truly matters: safety, efficiency, and innovation.
- Commitment to Continuous Improvement
- Lean Practices: Implement lean manufacturing principles to enhance productivity and eliminate inefficiencies.
- Feedback Loops: Regularly review performance and adjust strategies as needed.
- Emotional Intelligence
- Empathy: Understand and respond to the needs of employees, fostering trust and loyalty.
- Conflict Resolution: Handle disputes professionally to maintain a harmonious work environment.
Conclusion: Making a Difference
Great leadership in manufacturing goes beyond just meeting production quotas; it’s about making a meaningful difference in the lives of employees and the success of the organization. It’s a relentless pursuit of potential, armed with insight, courage, and tenacity. By embracing these principles, you will not only stand out as an effective leader but also drive your manufacturing organization toward success.
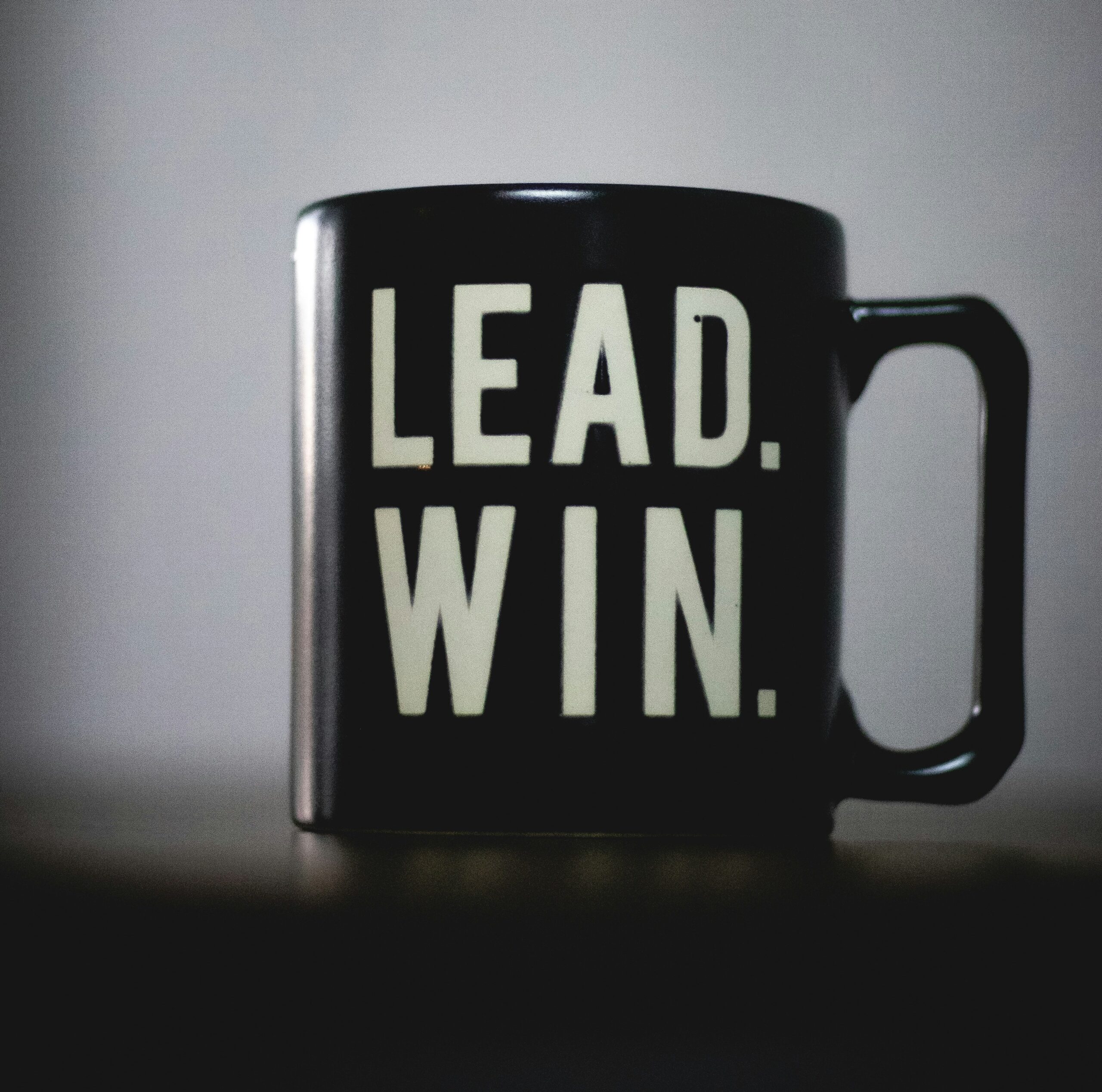